Integrating Systems Modeling with Simulation Helps Ensure Robust Space Debris Removal Mission
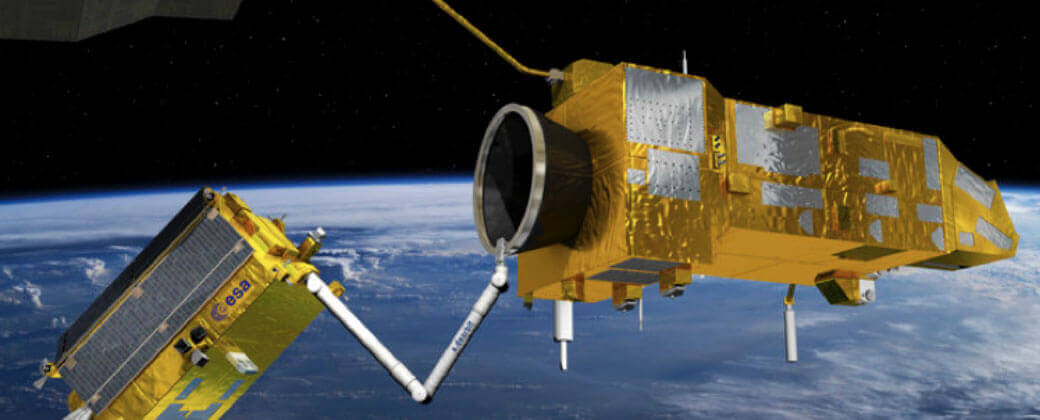
Executive Summary
- Industry: Aerospace
- Products: ModelCenter Integrate , ModelCenter Explore
- Applications: MBE: Model Based Engineering , MBSE: Model Based Systems Engineering
The European Space Agency (ESA) is studying an active debris removal mission called e.deorbit which is intended to capture an ESA-owned derelict satellite in low orbit and safely crash it into the ocean in a controlled atmospheric reentry. The Airbus Defence & Space proposal for this project used Model Based System Engineering (MBSE) to simultaneously define the mission requirements and the architecture. In a parallel internal study, Airbus engineers used ModelCenter Integrate and MBSEPak to integrate the simulation tools used to evaluate the performance of the architecture with the system model. This integration demonstrated that it is possible to greatly reduce the time required to verify the requirements and architecture by making it possible to run all the major simulation tools as part of an automated workflow that was driven by the systems model. This streamlined process increases the number of cases against which the entire system could be simulated by a several orders of magnitude. It also makes it possible to cycle through the simulation one time step at a time while simultaneously viewing simulation results for the entire mission. The result is that engineers have much more confidence in and managers and customers have a much better understanding of the proposal. “In future projects where systems modeling and simulation workflows are integrated from the beginning of the project, it should be possible to achieve significant improvements in mission performance, cost and leadtime,” said Stéphane Estable, Project Leader and System Architect at Airbus Defence & Space.
Background
Concept for future e.deorbit mission
The volume of space debris is continually increasing through a vicious circle in which collisions between individual objects generate additional debris which in turn leads to more collisions. ESA is studying a mission, scheduled for a projected launch in 2023, that will be the first time ever that debris are actively removed from space. A robotic arm and gripper riding on a custom spacecraft will capture the derelict satellite while operating autonomously with ground supervision. Many difficult obstacles need to be overcome to accomplish this mission including maneuvering autonomously towards the derelict satellite while avoiding collision and addressing countless potential mission environments and scenarios. Traditionally, Airbus engineers generate proposals for missions such as this by first writing out and validating the requirements and, when that process is completed, later developing the mission architecture. With this approach, problems with the requirements are frequently discovered while working on the architecture and these problems are often expensive to fix because interdependencies sometimes make it necessary to substantially revise the requirements and architecture.
Challenge
Use case diagram for typical mission activity
On the e.deorbit proposal, Airbus engineers addressed these concerns by using system modeling to simultaneously develop the mission requirements and architecture. They developed a SySML model that integrates the safety and architecture requirements, system capabilities, functional architecture and concept of operations (CONOPS). Developing the architecture and requirements in parallel helped to validate the requirements at an earlier stage in the project, saving considerable time and money. While this approach was a major step forward, Airbus engineers recognized that its benefits were limited by the fact that the domain simulations required to support the development of the architecture were each run manually and separately by engineers responsible for a particular domain. The results from these simulations were later uploaded to a database and used as input parameters for the system model and other simulations. The performance of the entire system for a particular use case is not clear until each of the simulations involved is completed which takes days or weeks. Considerable time and effort are required to simulate the performance of the entire system for even a single case, limiting the number of cases that can be run in the architecture definition phase. This creates the potential for errors and unexpected interactions that cost considerable time and money to correct when they are discovered later during the detailed design stage.

“The integration of system modeling and simulation at Airbus has had a high level of visibility and is considered to be a major success,” Estable concluded. “The objective is to iteratively implement a completely integrated process going forward in e.deorbit and other projects.”
Solution
Integration of system model with domain engineering models
Airbus used Phoenix Integration’s ModelCenter Integrate and MBSEPak to integrate the SYSML representation of the e.deorbit mission with the simulation tools that are used to predict the performance of architectural alternatives. Phoenix provided custom training and on-sight consulting to enable Airbus engineers to integrate the system model with the Simulink dynamic model used to determine the trajectories of the derelict and mission satellites, the cost model and many domain models used for avionics, structural and thermal simulation, among others. ModelCenter also manages the data flow between the simulation tools so the entire mission or any subsystem can now be simulated simultaneously in a single integrated process driven by a common dataset from the system model. Airbus engineers have the choice of cycling through the mission at time intervals of their choice and viewing the results after each step or simulating the entire mission in a batch process and viewing the results after the fact.
Benefit
Results
The integration between system modeling and simulation reduces the time required to simulate the complete mission by orders of magnitude. This makes it possible to examine thousands of cases instead of a few dozen cases that might normally be considered during the proposal stage. For example, the exact tumbling rate of the target satellite at the time of mission execution is unknown. The reduction in time required to simulate the entire system makes it possible to simulate the mission for a range of tumbling values to make sure the chosen architecture can support all eventualities. The ability to simulate the behavior of all subsystems together enables the study of unexpected interactions between the subsystems that cannot be identified in the individual simulations. The detection of these problems in the proposal stage makes it possible to correct them at a cost that can be orders of magnitude lower than would have been required to correct them later in the detailed design phase.
Optimizing spacecraft design
The integration of the system model and simulation models will have even greater benefits if Airbus’ design is funded for detailed design. A much larger number of simulations are required during this stage to optimize the design of the spacecraft with regards to objectives such as cost, power consumption, weight, and many other factors. The ability to run these simulations as part of an automated workflow will make it possible to utilize Phoenix Integration’s ModelCenter Explore to run automated parametric sweeps to traverse the design space and iterate to an optimized design based on goals set by Airbus engineers. Airbus performed an experiment to validate this methodology in an internal project independently of the e.Deorbit study. They looked at the tradeoff between reducing the mass of the structure by using lightweight but expensive materials versus using engines with higher specific impulse (Isp) and lower propellant consumption. “The integration of system modeling and simulation at Airbus has had a high level of visibility and is considered to be a major success,” Estable concluded. “The objective is to iteratively implement a completely integrated process going forward in e.deorbit and other projects.”