Submarine Hull Design Optimization
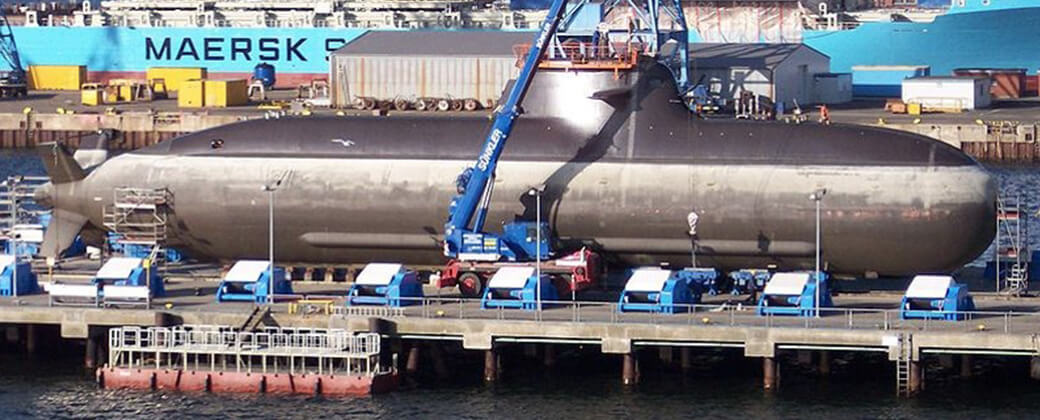
Executive Summary
- Industry: Defense
- Products: ModelCenter Explore , ModelCenter Integrate
- Applications: MDAO: Multi-Disciplinary Analysis and Optimization
Challenge
Minimize weight of submarine hull
At the request of a leading defense contractor, ModelCenter was used as a comparison for results already obtained in a submarine hull design study.1 Objectives were to minimize the weight and weight-to-displacement (volume) ratio of the German Type 212 class (U212) submarine hull subject to stress and athwart ship constraints (<20 ksi and <.0875 in, respectively)—using a previously modeled quarter-section baseline geometry preprocessed with Abaqus finite element analysis code. Variables in the Abaqus analysis consisted of 11 submarine shell thicknesses and 14 geometric quantities, such as stiffener frame spacing and cylinder lengths. The thicknesses and frame spacing were varied between specific enumerated ranges and the other geometric variables had low and high ranges imposed on them.
1Barner, Nicholas, “Isight-Abaqus Optimization of a Ring-Stiffened Cylinder”, 2010 SIMULIA Customer Conference, http://www.simulia.com/download/pdf2010/Barner_SCC2010.pdf
Solution
Use ModelCenter to Wrap Abaqus CAE file, Process Results and Perform Optimization
Abaqus CAE was used to re-generate and re-mesh hull geometry for the initial problem setup. While doing so, a Python script was recorded to capture the user’s actions. The Python script was then wrapped using ModelCenter Integrate’s QuickWrap tool. QuickWrap automatically exposed the variables in the Python script for all the thicknesses and geometry of interest, as well as a seeding quantity which governed the degree to which the mesh could be refined. The command to run Abaqus then simply took the Python script as an argument and performed the steps in the script. QuickWrap was thus able to create a ModelCenter component from an Abaqus CAE procedure. A calculator script was also written in ModelCenter to calculate the weight of the submarine (from total element volume and density), as well as the displacement (internal volume). ModelCenter Explore’s Darwin algorithm was used for optimization.
Benefit
Superior Results in Less Time plus Comprehensive Design Tradeoff Alternatives
The ModelCenter solution improved the submarine weight optimization with a 16.7% reduction in weight compared to the baseline study, and 16.3% improvement for the weight-to-displacement ratio. The ModelCenter approach automated iteration of 1,164 evaluations for the weight optimization and 1,361 evaluations for the weight-to-displacement optimization. If done manually, approximately 420 hours—10 minutes per evaluation not counting computer time—would have been required, whereas the ModelCenter approach took only 16 hours to setup the model and optimizer. In addition to the significant time savings, ModelCenter provided a much better design. Using Darwin, the ModelCenter approach not only found an optimal result but provided a tradeoff curve of possibilities. For example, the Pareto-optimal tradeoff between maximum stress and weight was found. A willingness to increase the weight of the submarine would result in less stress and the tradeoff curve would provide alternatives to achieve this design in a Pareto-optimal fashion.