Multilevel Optimization Reduces Cost of Building Wind Farm by Almost $4 Million
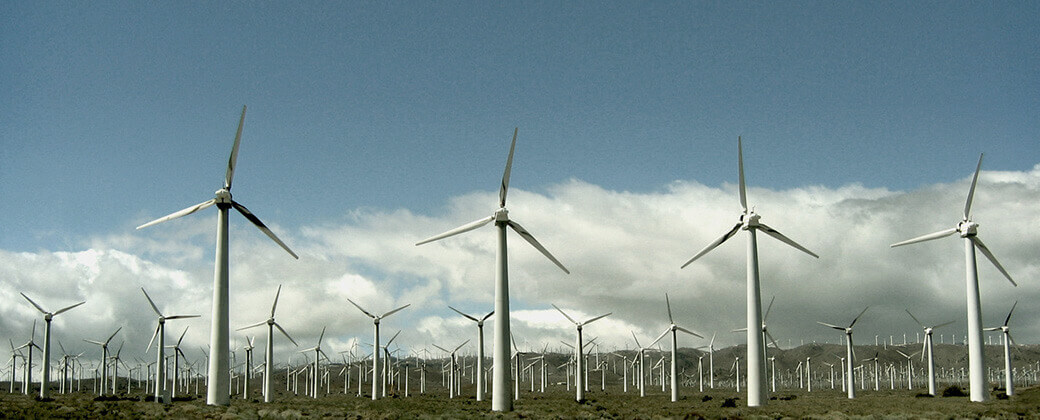
Executive Summary
- Industry: Energy
- Products: ModelCenter Integrate , ModelCenter Explore
- Applications: MBE: Model Based Engineering , MDAO: Multi-Disciplinary Analysis and Optimization
The Bobcat Bluff Wind Project, located in Archer City, Texas consists of 100 GE 1.5 MW turbines capable of producing up to 150 MW of electrical power. Like nearly all wind farm projects, it was designed in a sequential process, starting with positioning the turbines to maximize energy capture. Next, the roads used to construct the wind farm and the collection system used to carry power to the grid were designed to minimize construction costs. With this sequential design approach, the turbines were positioned without considering construction costs, resulting in higher than necessary construction costs. Stanford University consultants used this application to demonstrate how multilevel optimization with ModelCenter that simultaneously considers both energy capture and construction costs could have saved $4 million in construction costs and reduced the overall cost of energy produced by the wind farm by $0.20 per Megawatt hour. While this optimization was completed after the wind farm was built, the wind farm owner plans to use multilevel optimization to increase the profitability of future projects.
Background
The ideal wind farm design is dictated by a combination of technology and economics. The goals are usually to maximize energy production, minimize capital and operating costs, and comply with the constraints imposed by the site. The wind farm is typically laid out by considering various site sizes, site layouts, turbine types and hub heights. Of course, the optimum layout for the site is affected by design of the turbines used on the site and the optimum turbine design is also affected by the site layout. Spacing of wind turbines on the site must be considered carefully to avoid unacceptably high wake losses. The positioning of the wind turbines also has a major impact on construction costs by affecting the length of the roads that must be built or upgraded, the length of the transmission lines, and additional costs that are incurred for crossing streams and other obstacles. These design decisions and many others interact in very complex ways on the overall profitability of the wind farm.
Challenge
The owner of the Bobcat Bluff wind farm hired an engineering consultant to select and position the turbines to be used in the project. The consultants manually picked potential layouts based on experience and intuition and used OpenWind software to predict the energy they produced based on the wind data and topography of the site. The turbine design was then passed to the construction company whose engineers designed the infrastructure required for the development of the wind farm. Some new roads needed to be built and others required upgrading. Transmission lines needed to be built to carry power from each turbine to the substation. Additional costs were involved in both roads and transmission lines for crossing streams and a gas pipeline that traverses the site. The construction company engineers designed the infrastructure as best they could to minimize its costs. But some of the design choices that had been made in positioning the turbines drove up construction costs, such as by increasing the length of the roads and power lines that needed to be built. In most cases, it’s not practical for engineers working on the wind turbine layout to seek input from the construction company because designing an optimized road and power transmission system for even a single possible turbine layout is a major task involving weeks of engineering effort which is too slow considering that the turbine layout process might consider numerous alternative designs in a single day.

“ModelCenter is the only platform that I am aware of meeting the requirements of this application including the ability to integrate with multiple analysis packages and optimization routines,” Flager concluded.
Solution
Multilevel optimization process
Stanford University consultants performed a multilevel optimization on the Bobcat Bluff wind farm to demonstrate the savings that could be achieved by simultaneously optimizing energy capture and construction costs. They created a loop within the ModelCenter framework to automatically calculate the energy capture and the construction cost for any selected design point. The design point is defined by locating turbines on a rasterized image of the site that included only the areas that were feasible turbine locations. The areas that were excluded contained features such as structures, roads and wildlife areas. The consultants developed a wrapper for OpenWind that enabled ModelCenter to generate a turbine layout based on the map and execute an energy capture simulation to determine how much energy it would produce. The Stanford consultants then wrote a routine to optimize the construction costs for this layout that used an A* (pronounced A star) algorithm to plot efficient paths between the turbines for roads and power lines and an Esau-Williams algorithm to select the lowest cost combination of paths based on criteria selected by the Stanford consultants. The result was an optimized road layout and collection system for each layout. ModelCenter then populated an Excel spreadsheet with the energy capture and construction cost information to evaluate the overall profitability of the turbine layout.
The consultants developed a Greedy Stochastic algorithm as a ModelCenter plugin that drives the loop described above to optimize the turbine layout based on both energy capture and construction costs. This algorithm begins by analyzing a set of layouts that sparsely cover the complete design space. The algorithm then selects the locally most attractive layouts in each area of the design space without being concerned about the global rank of these layouts. The algorithm explores the design space around these layouts by creating new layouts in the same neighborhood and calculating their energy capture and construction cost. The algorithm continues exploring in each neighborhood, determining which direction to go based on whether each new layout is more or less favorable than its neighbors. “We selected this optimization approach because this problem is highly compute intensive and the Greedy Stochastic approach makes very efficient use of computing resources,” said Forest Flager, Research Associate and Lecturer, Center for Integrated Facility Engineering, Stanford University.
Bobcat Bluff as originally built
Bobcat Bluff optimized design
Benefit
Design alternative |
Construction cost |
Net energy |
Cost of energy |
As built |
$50,400,000 |
535.15 GWh |
$49.01 per MWh |
Optimized design |
$46,580,000 |
533.45 GWh |
$48.81 per MWh |
Bobcat wind farm savings
The optimization identified a turbine layout that offered much lower construction costs while capturing only slightly less energy than the design that was used to build the wind farm. The result was a savings of nearly $4 million in capital investment and a reduction in cost of energy of $0.20 per MWh over the lifetime of the wind farm. Stanford consultants used this same approach to optimize the Roosevelt wind farm which has a production capacity of 300 Megawatts. In this case, their optimized design reduced construction costs from $90,370,000 to $83,470,000, providing a savings of $0.22 per Megawatt/hour. “ModelCenter is the only platform that I am aware of meeting the requirements of this application including the ability to integrate with multiple analysis packages and optimization routines,” Flager concluded.